TECHNOLOGY
Tips for Laser Cutting Acrylic
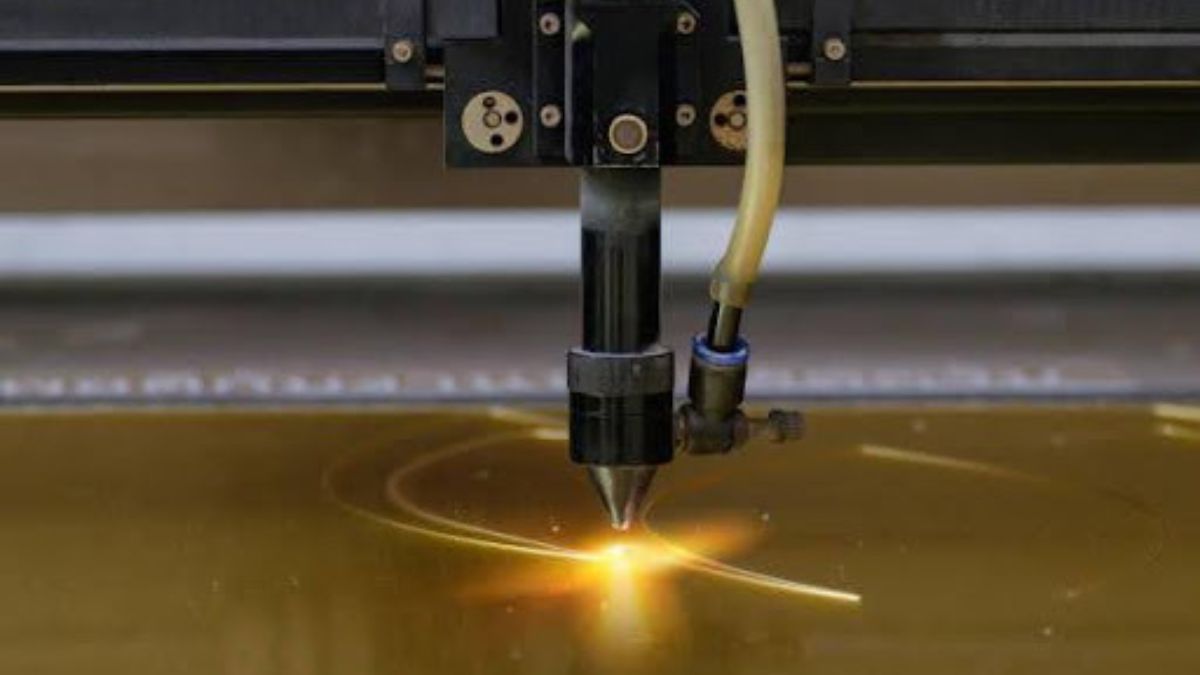
Laser cutting acrylic has become a favored option among both professionals and hobbyists due to its precision and capability to create complex designs. However, getting the best results requires more than just basic knowledge; it involves understanding the material’s properties, the laser cutting process, and the optimal settings for your machine. This article will provide valuable tips to help you get the most out of your laser cutting experience with acrylic.
How Does Laser Cutting Work for Acrylic?
Laser cutting offers a precise and efficient solution for cutting and engraving acrylic. Thus, understanding how laser cutting works for acrylic can help you achieve the best results.
Here’s a detailed look at the process:
The Basics of Laser Cutting Technique
Laser beam cutting uses a high-energy laser beam to penetrate or cut through materials. For acrylic, the laser beam is typically generated by a CO2 laser, known for its ability to produce clean cuts. When machining, fabricators direct the laser beam through a series of mirrors and lenses, focusing on a small, precise point on the acrylic surface. This concentrated energy allows for highly detailed and accurate cuts, so laser cutting is favored for intricate designs.
Interaction of Laser Beam and Acrylic
When the laser beam contacts the acrylic, it quickly heats the material to its melting point. The focused laser energy causes the acrylic to melt, vaporize, or burn away, creating a clean and precise cut. The key to achieving smooth edges and intricate designs lies in controlling the laser’s power, speed, and focus. Furthermore, understanding acrylic’s thermal properties helps fine-tune these parameters to avoid issues like excessive melting or charring.
Controlling Laser Parameters
You need to adjust several parameters on your laser cutter to optimize the cutting process. These include power, speed, focus, and frequency. For instance, frequency applies to some laser cutters as it determines the rate of laser pulses emitted per second. Adjusting the frequency can help achieve smoother cuts and better edge quality. For a CO2 laser, the frequency can be adjusted between 1,000 and 60,000 Hz.
Types of Acrylic for Laser Cutting
Two main types of acrylics are used in laser cutting – Cast acrylic and Extruded acrylic.
Cast Acrylic is preferred for laser cutting due to its clarity and ability to produce smooth, polished edges. Cast acrylic responds well to laser engraving, resulting in frosted white designs. Additionally, it offers better optical properties, making it suitable for high-quality applications.
While generally cheaper, extruded acrylic does not cut as cleanly as cast acrylic. It tends to melt more and produces a less polished edge. As such, extruded acrylic is better suited for applications where edge quality is less critical. Besides, its lower cost makes it a viable option for large-scale projects where precision is less of a concern.
Preparing Acrylic for Cutting
Before starting the laser cutting process, ensure your acrylic sheet is clean and dust-free. Surface contaminants can disrupt the laser beam and compromise the quality of the cut. Next, firmly secure the acrylic sheet on the cutting bed to avoid movement during the cutting process. Using masking tape on the acrylic can help protect the surface from smoke damage and keep the edges clean.
Safety Considerations
Laser cutting acrylic can produce fumes and particles that may be harmful if inhaled. Ensure your workspace is well-ventilated, and use an appropriate exhaust system to remove fumes. Wear personal protective equipment, such as safety goggles and masks, to protect yourself from potential hazards.
What Are the Best Settings for Laser Cut Acrylic?
Achieving the best results when laser cutting acrylic requires careful adjustment of various settings on your laser cutter. By optimizing these settings, you can ensure clean cuts, smooth edges, and minimal waste.
Check the detailed best settings to laser cut acrylic below:
Power Settings
The power setting controls the intensity of the laser beam. Generally, machinists employ higher power levels for cutting thicker acrylic, while lower power levels are better for engraving or cutting thinner sheets.
Overpowering can lead to excessive melting and charring, so finding a balance is crucial. Professionals often start with a lower power setting and gradually increase it until they achieve the desired cut quality. For instance, cutting 3mm thick acrylic requires 30-40 watts of laser power. In contrast, thicker sheets, such as 6mm, might need 50-60 watts to achieve a clean cut.
Speed Settings
Speed settings determine how fast the laser head moves across the acrylic. Faster speeds are suitable for engraving or cutting thin sheets because they minimize heat exposure and reduce the risk of burning.
For cutting thin acrylic sheets (up to 3mm), a speed of 15-20 mm/s is often effective. Thicker acrylic requires slower speeds, typically around 8-12 mm/s, to allow the laser enough time to penetrate the material thoroughly. Hence, adjusting the speed ensures a smooth cut without excessive heat buildup.
Frequency Settings
Frequency settings control the laser’s pulse rate and can also significantly impact cut quality. Lower frequencies (1000-5000 Hz) are ideal for cutting thicker acrylic, as they reduce the risk of overheating by producing fewer pulses per second. This setting helps achieve cleaner cuts without excessive melting.
Higher frequencies (at least 5000-20000 Hz) work better for engraving and cutting thin acrylic sheets. They provide more detailed work but increase heat buildup. As a result, professionals often adjust the frequency based on the specific acrylic type and thickness to optimize results.
Focus Settings
Proper focus is essential for achieving clean cuts. The laser beam should be concentrated at the correct depth within the acrylic. This is typically accomplished by adjusting the focal length to match the material’s thickness. Incorrect focus can lead to uneven cuts and poor edge quality. Professionals use focusing tools or manual adjustments to aim the laser correctly.
Air Assist
Air assist blows air over the cutting area, removing debris and cooling the cutting surface. This feature reduces the risk of flare-ups, improves edge quality, and keeps the cutting area clean. Typically, a flow rate of 0.5-1.5 cubic feet per minute (CFM) remains adequate for most acrylic cutting tasks.
What Is the Best Thickness of Acrylic for Laser Cutting?
Selecting the best thickness of acrylic for laser cutting depends on your specific project requirements, the capabilities of your laser cutter and the type of acrylic you are using.
Acrylic sheets come in various thicknesses, typically 1.5mm to 25mm or more. Each thickness serves different purposes and has advantages and challenges when it comes to laser cutting.
Here’s a detailed look at how to select the best thickness for your needs:
Thin Acrylic Sheets (1mm to 3mm)
Thin acrylic sheets are ideal for projects requiring fine details and precision. These sheets are easier to cut and engrave, making them perfect for applications such as jewellery, decorative items, and intricate signage. When cutting thin acrylic, lower power settings and higher speeds can help achieve clean cuts without excessive melting.
Medium Thickness Acrylic Sheets (4mm to 7mm)
Medium-thickness acrylic sheets offer a good balance between flexibility and durability. Cutting medium-thickness acrylic requires moderate power and speed settings. For example, a power setting of 40-50 watts and a speed of 10-15 mm/s are often practical for 5mm acrylic.
Thick Acrylic Sheets (8mm and above)
Manufacturers use thick acrylic sheets for structural applications. These sheets provide excellent strength and stability but can be more challenging to cut due to their thickness. High power settings and slower speeds are necessary to penetrate thicker acrylic. For instance, cutting 10mm acrylic might require a power setting of 60-80 watts and a speed of 5-10 mm/s.
How Do You Clean Acrylic After Laser Cutting?
Cleaning acrylic after laser cutting ensures your finished pieces look professional and polished. Proper cleaning removes any residue, dust, or smoke marks that can disfigure the appearance of your project.
Here are the steps on how to effectively clean acrylic after laser cutting:
Gather Your Supplies
You’ll need a soft microfiber cloth, mild dish soap, warm water, and a spray bottle. Steer clear of abrasive materials or caustic chemicals, as they can scrape or damage the acrylic surface.
Remove Dust and Debris
Gently wipe down the acrylic piece with a dry microfiber cloth before washing to remove any loose dust and debris. If you notice any stubborn particles stuck in intricate cuts, use a soft-bristled brush to dislodge them carefully.
Spray and Wipe
Next, prepare a mild dish soap with warm water in a spray bottle. Then, lightly spray the soapy water solution onto the acrylic surface. Be careful not to oversaturate, as excessive water can seep into minor cuts and edges, making it harder to dry. Using a clean microfiber cloth, gently rub the surface in a circular motion to eliminate any residue.
Rinse with Clean Water
After wiping with the soapy solution, spray a small amount of clean, warm water onto the acrylic to rinse off any soap residue. Again, use a clean microfiber cloth to wipe down the surface. Ensure all soap is removed, as leftover soap can leave streaks or a cloudy finish.
Dry the Acrylic
Dry the acrylic piece thoroughly with a dry microfiber cloth. Remove all moisture to prevent water spots. You can use compressed air to blow out any remaining water for intricate designs with tight spaces.
Polish for Extra Shine
If you want to give your acrylic piece an extra shine, you can use a plastic polish specifically designed for acrylic. Apply a light polish to a clean microfiber cloth and gently buff the surface using circular motions. This enhances the shine and helps protect the acrylic from future scratches.
Conclusion
Laser cutting acrylic can elevate your projects with its precision and versatility. Achieving the best results involves understanding how laser cutting works, selecting the appropriate settings, and choosing the right acrylic thickness. Proper cleaning after cutting ensures your pieces look well-polished. By adhering to these tips, you can smoothly improve your laser cutting process and fabricate superb acrylic items.
TECHNOLOGY
The Best Door for Your AC Closet: Cool Choices That Make a Difference
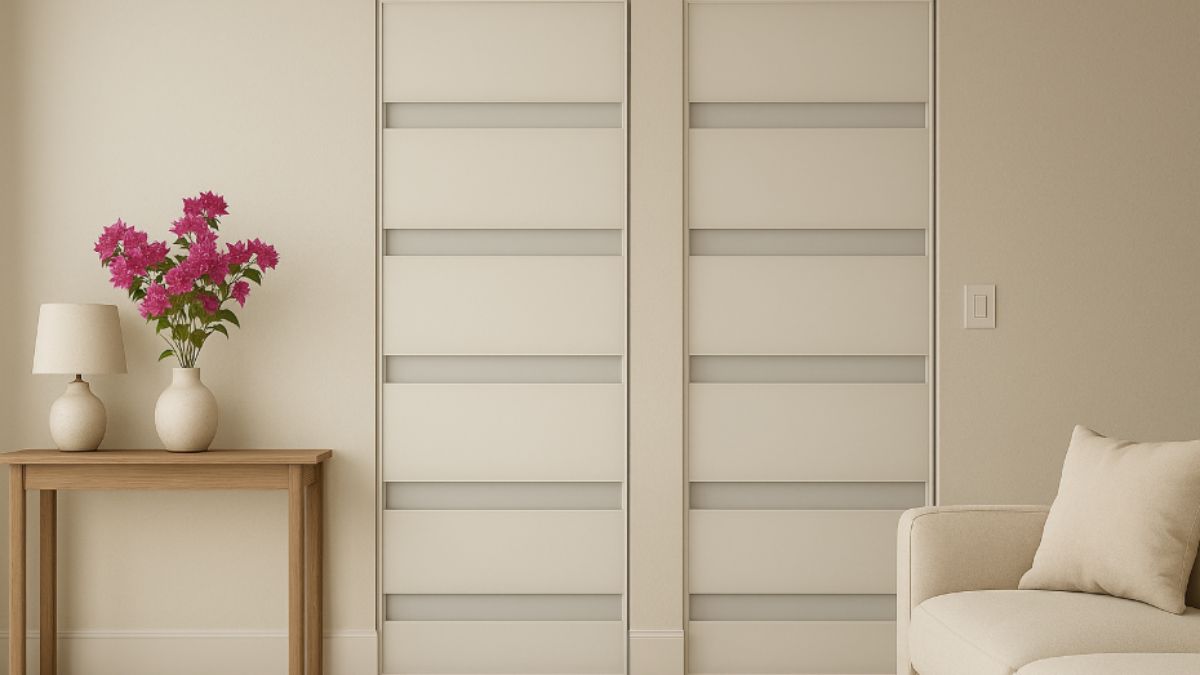
Whether you’re an outdoorsy type who loves a good disc golf course or someone who just appreciates a chill, comfortable indoor vibe after a long day in the sun, one thing’s for sure: a well-cooled home matters. But what most people don’t think about is that even something as simple as the door on your AC closet can make a big impact on your system’s efficiency, longevity, and even your electric bill.
Choosing the best door for your AC closet isn’t just about looks — it’s about airflow, access, and avoiding mold and maintenance nightmares down the line. If you’re living in Florida or any other high-humidity, high-heat zone, it’s even more critical to make the right choice. And for that, check out these manufacturers of custom AC closet doors in Florida — they know how to handle the heat.
Why Your AC Closet Door Actually Matters
Most people ignore their AC closet. It’s the closed-off, humming corner of the house that only gets attention when something breaks. But here’s the deal — your AC unit needs proper ventilation to work effectively. If your door doesn’t allow for airflow, you risk trapping heat, overworking your unit, and creating the perfect storm for mold and mildew buildup.
Not to mention: the wrong door can make repairs a nightmare. Imagine wrangling with a bulky slab door just to replace a filter. No thanks.
Top Features to Look For in an AC Closet Door
Here’s what makes an AC closet door great:
- Louvered Panels: These slatted vents allow air to circulate freely while keeping the unit hidden from view.
- Moisture-Resistant Materials: Especially important in coastal or humid areas. MDF or low-grade wood just won’t cut it.
- Easy Access Design: Think bi-fold or double doors. You want a door that opens wide enough for maintenance without bumping into walls or furniture.
- Sound Dampening: A quality door helps muffle that constant AC hum, giving your home more peace and quiet.
If you’re after a door that hits all these marks — built to size, designed for airflow, and built to last — look no further than APA Closet Doors. They specialize in custom solutions that don’t just function well — they look good doing it.
The Best Styles for Different Homes
Depending on your home’s layout, here are some top recommendations:
- Small Spaces: Bi-fold louvered doors are a space-saving, efficient option.
- Modern Interiors: A sleek full-louver door in clean white or gray blends beautifully into minimalist homes.
- Rustic Vibes: Opt for wood-look composite doors with subtle louvers for a farmhouse-chic aesthetic.
- Rental Units: Durable PVC louvered doors are budget-friendly and easy to replace or clean.
Final Thoughts: Don’t Sweat the Small Stuff — Upgrade It
Choosing the best AC closet door might seem minor, but it’s one of those small upgrades that makes your home run smoother and look better. Plus, it helps your AC breathe a little easier — and that means fewer breakdowns and lower bills over time.
If you’re already sweating your setup, maybe it’s time to let the airflow in and give your AC unit the ventilation it deserves.
TECHNOLOGY
YWMLFZ 48W Cordless: Features That Make It Stand Out in the Market
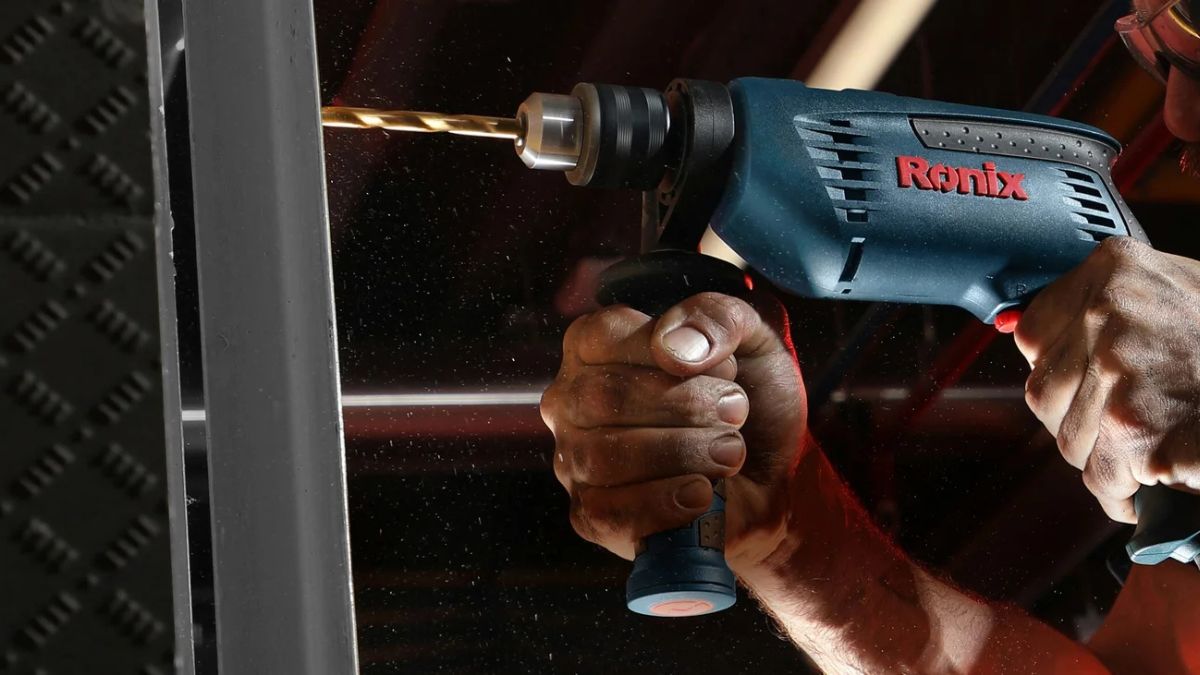
Introduction to the YWMLFZ 48W Cordless
When it comes to cordless tools, the YWMLFZ 48W Cordless has carved a niche for itself that stands out in today’s competitive market. This tool promises not only power and performance but also innovative features that cater to both DIY enthusiasts and seasoned professionals alike. Imagine tackling projects with ease, thanks to a design that prioritizes user comfort while delivering impressive battery life. Curious about what makes this tool so special? Let’s explore its standout features and see why the YWMLFZ 48W Cordless should be at the top of your must-have list!
Power and Performance
The YWMLFZ 48W Cordless is engineered for exceptional power and performance. With its robust motor, this tool delivers a reliable output that meets the demands of various tasks with ease.
Users will appreciate the impressive torque, which allows it to tackle heavy-duty projects without breaking a sweat. Whether you’re drilling into tough materials or driving screws efficiently, this cordless tool rises to the occasion.
Moreover, the lightweight design does not compromise its strength. It maintains balance while providing maximum efficiency in every application.
You can expect consistent results from start to finish, ensuring your projects are completed smoothly. The synergy between power and performance sets the YWMLFZ apart in its category, making it an essential addition to any toolkit.
Innovative Design and Ergonomics
The YWMLFZ 48W Cordless showcases an innovative design that prioritizes user comfort and efficiency. Its sleek body is not just about aesthetics; it’s engineered to fit comfortably in your hand, reducing strain during extended use.
With a lightweight construction, this tool allows for easy maneuverability. Whether you’re working on intricate tasks or tackling larger projects, the ergonomic grip ensures you maintain control without tiring out your wrist.
Every detail has been considered. The intuitive layout of buttons and controls means less fumbling around and more focus on the task at hand. This thoughtful approach enhances productivity while keeping safety in mind.
Additionally, its compact size makes storage a breeze, fitting neatly into any toolbox or shelf space. The combination of functionality and ease-of-use sets the YWMLFZ apart from other tools in its class.
Long-Lasting Battery Life
The YWMLFZ 48W Cordless shines with its impressive battery life. Users will appreciate the efficiency that allows for extended use without interruptions.
Equipped with advanced lithium-ion technology, this cordless tool ensures consistent power output throughout its runtime. You can tackle tasks confidently, knowing you won’t run out of juice mid-project.
Charging is quick and hassle-free. A full charge means hours of work, making it an ideal choice for both professionals and DIY enthusiasts alike.
Whether you’re working on intricate details or larger jobs, the longevity of the battery supports your needs seamlessly. There’s no need to worry about constantly recharging during important projects—just grab your YWMLFZ and get started!
Versatility and Ease of Use
The YWMLFZ 48W Cordless truly excels in versatility. Whether you’re tackling home repairs, crafting projects, or professional tasks, it adapts seamlessly to your needs. Its wide range of attachments makes switching from one job to another a breeze.
Ease of use is at the forefront of its design. The intuitive controls allow even beginners to operate it with confidence. You won’t waste time fumbling around; you can focus on what matters—getting the job done efficiently.
Its lightweight frame means less fatigue during extended use. Plus, maneuvering in tight spaces becomes effortless with this tool’s compact size.
You’ll appreciate how quickly it charges and how readily it’s available when inspiration strikes or urgency calls for action. The YWMLFZ 48W Cordless is crafted for those who value efficiency without sacrificing quality in every task they undertake.
Customer Reviews and Feedback
Customer reviews for the YWMLFZ 48W Cordless highlight its reliability and efficiency. Users frequently praise its powerful performance, noting that it handles various tasks with ease.
Many customers appreciate the lightweight design. This feature makes extended use less tiring, allowing them to tackle projects without discomfort. The ergonomic grip also earns positive remarks for enhancing control during operation.
Battery life is another standout point in feedback. Users report being able to complete multiple jobs on a single charge, making it ideal for both home and professional settings.
Additionally, buyers love its versatility across different applications. From DIY enthusiasts to seasoned professionals, many express satisfaction with how well this tool adapts to their needs.
Specific comments about customer service also reflect positively on the brand’s commitment to user satisfaction, further bolstering confidence in choosing this model over others in the market.
Comparison with Other Cordless Tools in the Market
When it comes to cordless tools, the market is saturated with options. However, the YWMLFZ 48W Cordless truly sets itself apart from competitors.
Many popular brands offer similar wattage or features. Yet, they often compromise on battery life or ergonomics. The YWMLFZ maintains a perfect balance between power and comfort.
While some tools feel bulky in hand, this model boasts an innovative design that prioritizes user experience. It enhances precision while reducing fatigue during lengthy tasks.
Price points vary significantly among rival products. The YWMLFZ offers exceptional value without sacrificing quality or performance. This makes it an attractive option for both amateurs and professionals alike.
Customer feedback consistently highlights its reliability compared to other models in its category. Users appreciate how seamlessly it integrates into their toolkit without any hassle.
Conclusion: Why the YWMLFZ 48W Cordless is a Must-Have for Your Tool Collection
The YWMLFZ 48W Cordless stands out in a crowded market for several compelling reasons. Its impressive power and performance make it suitable for various tasks, from intricate projects to heavy-duty jobs. The innovative design ensures comfort during extended use, making it appealing for both professionals and DIY enthusiasts.
With long-lasting battery life, you won’t have to worry about interruptions while working on important projects. This tool’s versatility allows you to tackle different applications with ease, enhancing your productivity significantly.
Customer reviews consistently highlight satisfaction regarding its user-friendly features and reliable performance. When compared to other cordless tools available today, the YWMLFZ 48W shines due to its combination of quality and affordability.
For anyone looking to enhance their toolkit with a dependable instrument that delivers exceptional results, the YWMLFZ 48W Cordless is undoubtedly worth considering. It represents an investment in efficiency and effectiveness that no serious craftsman or hobbyist should overlook.
TECHNOLOGY
Innovating Industry: The Future of Metal Casting Solutions
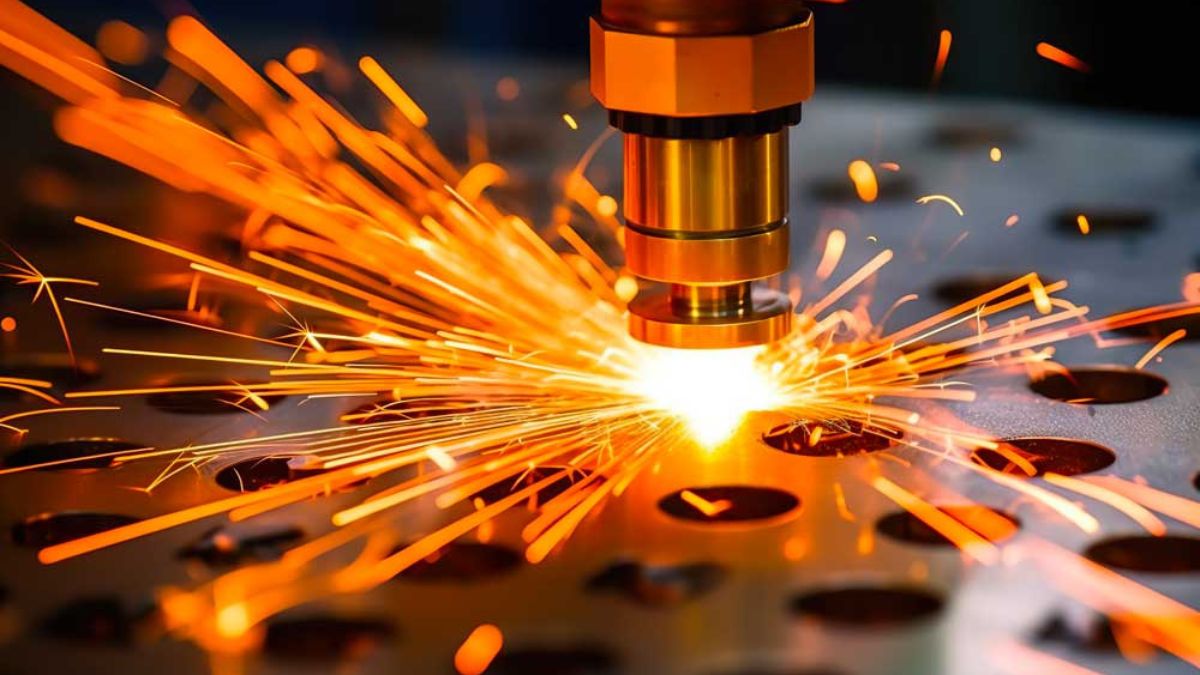
The relentless drive for industrial innovation has always been at the core of manufacturing development. In the field of metalworking, this quest for progress is epitomised by the continual advancement of casting solutions. Metal casting stands as one of the vital processes in the manufacturing world, bridging the gap between the design of complex components and their real-world applications. As we look towards the future, the metal casting industry prepares itself for a suite of transformative changes.
Digitisation of Casting Processes
The emergence of digital technologies is revolutionising countless industries, and metal casting is no exception. The integration of advanced software for design, simulation, and process control is enhancing precision, efficiency, and repeatability in casting operations. Future casting solutions will likely leverage even more sophisticated digital tools, enabling foundries to produce components with stricter tolerances and higher complexity.
Sustainability and Environmental Responsibility
The global conversation on sustainability has left an indelible mark on manufacturing practices. As a result, the metal casting industry is increasingly focusing on reducing its environmental impact. This encompasses not only the efficient use of resources and energy but also the adoption of renewable energy sources and recycling of materials. Innovations in this space will shape a new image for metal casting, one that is harmonious with environmental stewardship.
Advanced Materials and Alloys
Material science perpetually unlocks new potentials for various industries, and metal casting will benefit immensely from the development of novel materials and alloys. The future will see the propagation of lightweight metals with high-strength properties, catering to sectors such as aerospace, automotive, and defence. These advanced materials will demand equally advanced casting solutions capable of handling their unique characteristics.
Automated and Robotic Systems
Automation is no stranger to manufacturing, yet its potential in metal casting has not been fully exploited. The future promises a broader adoption of robotic systems that perform tasks with higher precision and consistency. Automation will not only improve production rates but also uphold stringent quality standards, minimise waste, and reduce the potential for human error.
Customisation and Personalisation
As consumer and client demands veer towards customisation, industries have to adapt to offer greater personalisation in their products. Metal casting is poised to meet these demands through flexible manufacturing systems that can accommodate variations in design without sacrificing efficiency. This increased flexibility will usher in a new era for the industry, one where small-batch, bespoke products are as viable as mass-produced items.
Collaborative Industry Relationships
Critical to the growth and adaptation of the metal casting industry are the relationships forged between foundries, designers, engineers, and end-users. Collaboration facilitates the exchange of ideas, the pooling of resources, and the development of innovative casting solutions that meet or exceed market needs. As these bonds strengthen, the industry as a whole can more effectively tackle the challenges ahead.
Enhancing Workforce Skills and Education
Technological advancements necessitate a workforce that is skilled in new and emerging fields. Future developments in metal casting will require an emphasis on education and skill-building within the industry’s workforce. Training programs and partnerships with educational institutions will ensure that the next generation of metal casters is equipped with the knowledge and expertise required for the industry’s evolution.
Quality and Regulatory Standards
In an increasingly global market, the adherence to international quality and regulatory standards becomes even more critical. Future metal casting operations will need to be compliant with a variety of standards to ensure market access and consumer trust. Innovations within the industry must balance the drive for efficiency and cost-effectiveness with rigorous quality control mechanisms.
Leveraging Big Data and Analytics
The colossal data generated by modern manufacturing processes holds invaluable insights into efficiency and productivity. By leveraging big data and analytics, future casting solutions can optimise every aspect of their operations, from resource allocation to process parameters, and from defect detection to predictive maintenance. Such data-driven approaches will be instrumental in achieving new heights in manufacturing excellence.
Adaptive and Responsive Supply Chains
A well-integrated and responsive supply chain is vital to the success of any manufacturing endeavour, including metal casting. As industries evolve, so too must the supply chains that support them. Innovations in logistics, inventory management, and supplier relationships will enable casting companies to react swiftly to market shifts and demands.
Expanding the Capabilities of Additive Manufacturing
Additive manufacturing, or 3D printing, has already begun to impact the metal casting industry. As this technology matures, it will not only serve as a complement to traditional casting methods but also expand the possibilities for design and manufacturing. Complex geometries that were once impossible to cast may become routine, enabling the creation of components that are lighter, stronger, and more efficient.
Enhancing Collaboration with CAD/CAM
The integration of computer-aided design (CAD) and computer-aided manufacturing (CAM) systems streamlines the transition from design to production. As these tools become more potent and user-friendly, their role in facilitating collaboration and reducing lead times in the casting industry will become even more pronounced.
Adapting to Emerging Markets and Needs
As new markets emerge and existing ones evolve, the metal casting industry must remain agile and responsive. This calls for casting solutions that not only address current requirements but also anticipate future trends. Those who are agile in responding to changes in consumer expectations and technological possibilities will thrive in the dynamic landscape of manufacturing.
The Importance of Continuous Innovation
It is undeniable that the future of metal casting hinges on continuous innovation. As industries worldwide become more complex and interconnected, the need for cutting-edge casting solutions that drive efficiency, sustainability, and quality grows ever stronger. By embracing these technological shifts, the metal casting sector can cement its position as a pillar of modern manufacturing, breathing life into the products and infrastructures that define our everyday existence.
Indeed, the industry’s future is bright with promise, fueled by advancements in technology and a commitment to sustainable practices. As businesses and individuals alike look towards the new possibilities on the horizon, they turn to innovators and industry leaders for advanced casting solutions that will help them realise their most ambitious projects. With these technological leaps, metal casting is set to remain a core component of the global manufacturing landscape for years to come.
-
TECHNOLOGY3 weeks ago
Top 10 Must-Read Stories from Kristen Archives You Can’t Miss
-
TECHNOLOGY6 months ago
Sky Bri Net Worth Revealed: How She Built Her Financial Empire
-
TOPIC8 months ago
Basement Renovation Contractors: How They Tackle Structural Issues During Renovations
-
TOPIC3 months ago
5 Reasons the //Vital-Mag.Net Blog Dominates Lifestyle
-
TOPIC1 month ago
Top 10 Articles from the ://Vital-Mag.net Blog That You Can’t Miss
-
CRYPTO5 months ago
Crypto30x.com Review: Is It the Right Platform for You?
-
BUSINESS3 weeks ago
TraceLoans Explained What You Need to Know
-
BUSINESS1 month ago
Decoding the Kennedy Funding Ripoff Report: Facts vs. Fiction